Neptune Plumbing & Heating Co. reduces manual data entry errors and enhances product traceability with a Jonas eMobile barcode scanning integration.
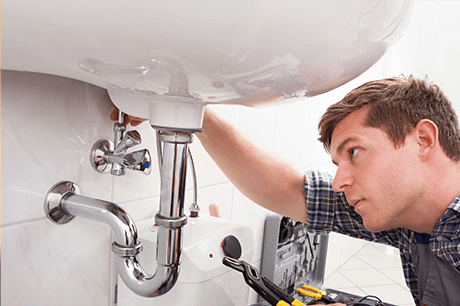
The Company
Neptune Plumbing & Heating Co. of Cleveland, OH, specializes in commercial, industrial, and institutional plumbing. Since 1957, the company has experienced success by serving local businesses, from corporate offices and retail shops to apartment complexes, health care facilities, and government institutions.
The Challenge
The technicians at Neptune Plumbing carry a significant parts supply in their service trucks. This means that the techs require the ability to manage and charge parts, on site, with precision and efficiency.
Early on, Neptune Plumbing recognized they needed a solution to help automate the management and fulfillment of their plumbing work orders. So, they made the business decision to use Jonas’s eMobile solution, with success. However, on smaller devices, the manual process of entering parts in eMobile was prone to typing errors and incorrect selection of part numbers. This meant that, particularly in time-sensitive situations, typing errors were made and wrong parts were retrieved from the inventory.
“When searching for parts in eMobile, techs were occasionally challenged to find the correct parts due to the formatting of the part’s name or the way the name was entered into the Jonas Inventory, said Adam Wallenstein, Neptune’s President. He continued, “In some instances, the techs had to call the office to confirm the correct part description, which was less efficient.”
The Solution
Neptune Plumbing decided to rethink their approach to managing and charging parts to improve the efficiency and accuracy of part selection in the field. After a conversation with the Jonas Construction team, Neptune decided to use the eMobile and Pic2Shop integration. Pic2Shop is a 3rd-party, barcode scanning application that is supported by eMobile through native integration. Pic2Shop extends eMobile’s capabilities by enabling the ability to scan barcodes while managing and charging parts on site.
As expected, Neptune did their due diligence to ensure the extended capabilities met their requirements. Neptune’s IT team installed the Pic2Shop application on their techs’ remote devices, enabled the integration with eMobile, and performed additional security checks to ensure it met their security standards. In addition, Neptune Plumbing reached out to their parts vendors for barcode books that the techs use to reconcile parts in their trucks.
As a result, all Neptune techs are now using barcode scanning for all of their parts identification while on site. This meant no more typing errors and no more calls to the back office to double-check part names.
The Result
By implementing barcode scanning while on site, Neptune Plumbing significantly increased their accuracy in billings and parts replenishment. Wallenstein confirmed, “The transition to this new process was simple and the parts management in eMobile is now super easy. The overall accuracy of parts being selected is close to 100%.”