Last Updated on July 17, 2023
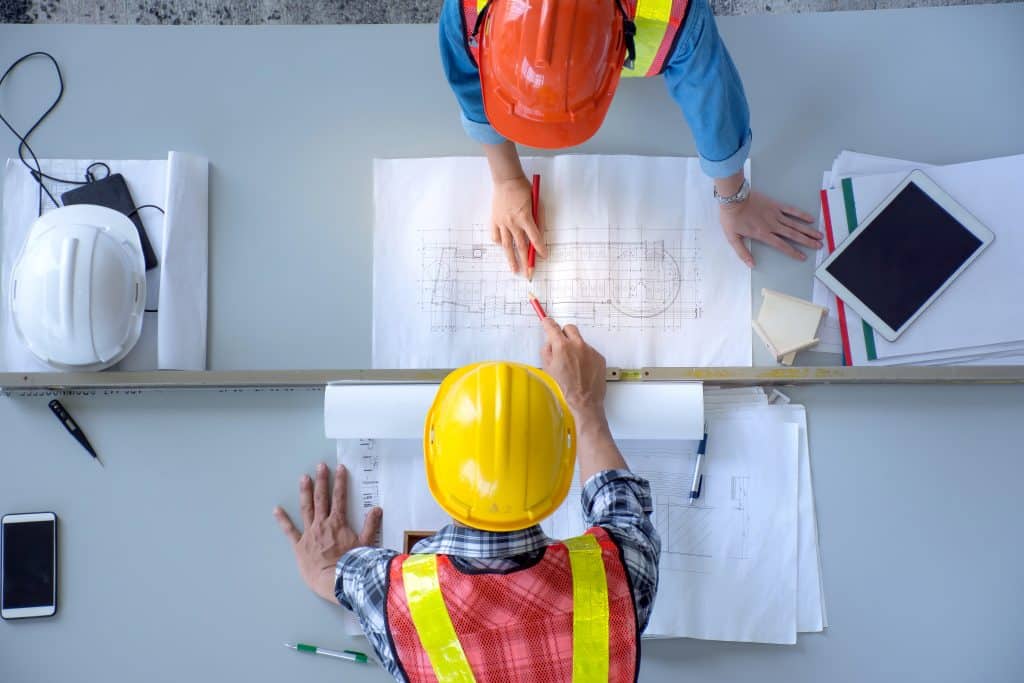
If you are a construction manager, you know one, employ one, or report to one, this article is for you!
The challenges that construction managers face start and end with the schedule.
The schedule gives direction, it adheres to requirements, and most importantly, it sets expectations. A seasoned construction manager will understand the true value of a schedule and use it to their advantage.
This article outlines the essential steps in building an efficient and realistic construction schedule that will support, and not hinder, your project goals. But before we move on, let’s identify what a construction schedule is, and what makes it “good”!
What is a Construction Schedule?
A construction project schedule is, in a sense, the path laid out before us, that helps us get to where we want to go. It helps us establish the most efficient method for completing the project. Construction schedules come in many forms, from standard excel-based ones for smaller jobs to elaborate, comprehensive schedules created using construction project management software.
As we think about our next schedule, and what it entails, it’s important to consider what makes a good construction schedule, and knowing what to avoid when constructing it.
What Makes a Good Construction Schedule?
- It acts as a map – The schedule meets the contract milestones and provides the team with the map to follow in order to get the job done.
- It shows dependencies – It breaks down the project into detailed tasks and prioritizes these tasks based on dependencies between them.
- It is achievable – It aligns with the deadlines and with the available resources, such as equipment and personnel.
- It’s proven – It draws from past experience to estimate the task efforts.
- It provides timely information – A schedule can be used to monitor the progress of subcontractors and suppliers.
As you can see, construction schedule is more than a “to do” list of things than you need to complete in a sequence. It incorporates everything from resources, timing, approvals, so the risk of missing things is high. Your scheduling efforts can be undermined if your schedule…
- Doesn’t handle resources – The schedule doesn’t account for available resources.
- Doesn’t consider locale – The schedule doesn’t take into account issues associated with typical weather conditions for a particular region (ie: heat, rain, snow).
- Doesn’t consider prerequisite tasks – It doesn’t allow sufficient time for procurement, design manufacturing, permits, and approvals.
- Doesn’t include operational facility requirements, such as power or water supply.
The construction schedule is an important tool to map construction projects. Now that we know the good and bad signs of construction schedules, it’s time to dig into the steps you should take as you prepare your for your project.
How Do You Create a Construction Schedule?
Your construction schedule is a complete blueprint of how a project will be completed and by when. It outlines project timeframes and milestones, tracks the project progress, and helps you and your team keep everything on time and on budget.
Creating a construction schedule can be a time-consuming job. That said, it it worth every penny and will save time along the way. It helps avoid issues and manages project resources, including time, efficiently. Let’s dig a little deeper…
Step 1. Gather Information About Project Requirements
Too often, unsuccessful projects end with someone saying “The requirements weren’t clear.” Still, this is the most important question and it may be seen as too obvious to ask.
For example, a statement like “let’s build a hotel” doesn’t make a good requirement. Proper requirements define the functions the building going to serve. What kind of hotel? Which specializations should be taken into account? How many visitors should it cater for? Answers to these (and a lot more other!) questions is a good starting point.
Keep in mind that as you gather your requirements, they may stand to change throughout the project. Planning ahead will allow you to have more time to modify requirements as your project evolves.
Step 2. Choose Your Scheduling Technique
By sticking to a specific scheduling method, you can save yourself from hassles, disputes, and conflicts. Here are the most common construction scheduling techniques you can choose from, depending on your project requirements:
- Gantt chart: This is probably the most effortless way to set up a schedule. Invented in the 1910s, Gantt charts are popular in the construction industry for their ease of use and versatility. Gantt charts present a list of activities, dependencies between activities, and the activity status.
- Critical Path Scheduling is more detailed than Gantt charts. The schedule splits the activities into segments, with activity shown as a “path” with start and end dates. The focus of this scheduling technique is to let everyone know what tasks must be completed before others can be started, ensuring work follows a “critical path”.
- The Line of Balance Scheduling method is generally used for repetitive jobs. The schedule specifies the exact amount of resources required for every stage of the project. This method is often used in road construction, as well as construction in general.
- Q Scheduling can refer to two different methods. First, a Quantitative Schedule refers to the quantities produced during various stages of the project. The second is Queue Scheduling. This method requires two tasks to be completed in exact sequence so that they don’t overlap each other.
- The Resource-Oriented Scheduling method focuses on the resources required to complete the project. This type of scheduling is often used in projects requiring minimal or unique resources, most often, when managing multiple projects with fixed resources of staff or equipment. For example, a design office has a limited number of staff which must be assigned to particular design activities. When the workload grows, the designers may fall behind on completing their assignments.
Depending on the nature of your construction project, it may be a good idea to combine some of these scheduling techniques to improve your efficiency and productivity.
Step 3. Identify & Prioritize Project Tasks
Throughout a project, you may notice, or even expect, priorities to change as the project progresses. Task prioritization becomes a priceless task that pays you back in added efficiency. There are a few different methods that can help you prioritize. Here are a few of them:
First of all, you may prioritize features according to their cost. This method is useful when a construction project has a fixed budget and finances are scarce. With this method, the benefit is that you keep costs down, but on the flip side it may leave you with important tasks outside your scope.
The second option is to prioritize customer requirements. This method calls for identifying the critical functions of the project and prioritizing the tasks in such a way that you complete these functions first. For example, your new construction may not need landscaping immediately, but ventilation and lighting are crucial. These critical tasks must be completed first. Note, you should keep an eye out for mission-critical tasks, left unidentified by the customer.
The third popular method requires you to evaluate the available resources. For example, you may have limited skilled manpower or a short supply of specific construction materials. Under certain circumstances, you should prioritize the tasks for which you have enough labor and supplies. Later on, if the budget permits, you can hire more people and find the materials you need.
Putting one, or more, of these methods into practice, you’ll never wonder what to work on first again!
Step 4. Identify Potential Constraints
Project constraints, or limitations, are inevitable, especially in construction where multiple parties are involved.
First of all, let’s recognize the potential constraints you may be facing. The following limitations are called “The Iron Triangle,” and for a good reason:
- Time: The expected project completion date.
- Scope: The expected results of the project.
- Budget: The amount of money allocated to complete the project.
When not managed, constraints can develop into conflicts and disputes, which bring additional costs. It can sound impossible, but in most cases, limitations of constraints can be reduced or eliminated with an approach that is timely and methodical. Identifying the potential constraints early in a construction project will help to decrease the unwanted loss of both money and time because of inadequate planning.
Step 5. Estimate Task Duration & Timeline
What happens when you don’t estimate the duration of a project task correctly?
In addition to the obvious – that your project may run long – there are cost and resource implications that will likely impact your revenue.
At best, you or your entire team are facing overtime. At worst, errors in project duration can result in insufficient budgets, loss of profits, and disappointed stakeholders or customers.
Estimating task duration is a critical piece of a puzzle. This is the process of determining the amount of time required for a project activity using the available resources.
Knowing individual task duration is the first step in building the overall project timeline. To estimate the duration of your project’s tasks, you can use five common ways:
- Look to the past and estimate how long it took for a similar task to be completed. Use timelines and reports to make a well-informed estimate.
- Three-point estimating: Consider best and worst-case scenarios. The best-case scenario is the time it would take if everything goes according to the plan. The worst-case scenario is the time it would take if everything goes wrong. Most often, your final number will fall somewhere in the middle.
- Group decision making: This method calls for the collective wisdom of your team leads, thus eliminating individual biases. You may use a decision approved by the majority, for example, asking to pick a time for “Concrete pouring” and choose from 4, 6, or 8 hours. You can also use a Delphi Method when each group member makes an estimate independently, then the results are compiled and the decision is made.
- Though not all work can be estimated using this method, there’s even a simpler and quicker way: Multiply the quantity of work by the number of hours required to complete it. For example, if a painter can paint 100 square feet in one hour and you have 6,000 square feet to paint, you can calculate that this task will require 60 hours of work.
When it comes to choosing the units of the duration, choose whatever works best. For small projects, less than two weeks in duration, tracking in hours works best. Larger projects will need to be tracked in days or they may get bogged down by smaller units.
Step 6. Allocate Tasks to Team Members
Resource allocation is crucial for the success of the project. These resources include money, equipment and machinery, building materials, technology, and your workforce.
Once you have identified all the tasks that are needed to complete the project, along with the duration, you need to allocate tasks among your team members. Take into consideration the project scope, task dependencies, and resource dependencies as you do this.
At the end of this step, each team member should understand what they are responsible for. This will prevent the overlap of responsibilities that can cost money and cause confusion. For example, engineers need to make field visits to confirm that the engineering specifications – their responsibilities – are being adhered to. This is not the job of the architect or contractor.
Plan Resource Allocation
The Pulse of the Profession survey reveals that 23% construction project managers blame inadequate resource allocation as the primary cause of project failure.
During the resource allocation step, the project manager assigns and schedules resources in the most cost-effective way possible. Here are the essential things to keep in mind:
- List and document your resources: Start with the workforce allocation plan to spot skills gaps and speed up recruitment depending on project demand.
- Identify potential red flags: Keep your eye on the risks and and figure out different ways to respond to them ahead of time.
- Develop a clear modification process: This helps to reduce the change order response time and also to create contingency plans.
One thing to be aware of is the over-allocation of resources. This happens when you assign more project tasks than your team members can handle. If your team members are assigned to various tasks, make sure they aren’t being spread too thin.
Another best practice is to step up your time tracking methods. A detailed record of work being done ensures you stay on budget with resources. Tracking performance will also help you designate the right tasks to the right people.
Step 8. Adjust, Adjust, Adjust!
Once the project is already underway, making changes to the schedule is possible – to an extent. It’s more cost-effective to make any major structural changes during the design phase, not during the construction phase. But if you are still feeling overwhelmed and adjustments are necessary, then the following steps can help:
- Change the scope of the project (up or down) or add resources – but keep in mind that this way always means more cost, so this should be agreed upon with stakeholders.
- Add more time to a task, split a task in two, or modify resource usage. You can also adjust the dependencies between tasks to allow some of the work to happen in parallel.
- You can also move a task to a time slot when more resources are available but this may mean re-calculating the entire project schedule so that the adjustment doesn’t affect the critical path of work.
- Negotiate additional time, however, a later completion date may also mean budget increase. Again, this is something to be agreed upon with key project stakeholders.
Making adjustments when the project is well underway can be challenging. That said, there are tools available that can help you throughout the entire project process – read on!
What is the Best Construction Scheduling Software?
With so many moving parts – people, equipment, materials, and more – an accurately mapped schedule is indispensable. Managing construction projects and allocate resources efficiently can be a challenge without construction scheduling software. However, a generic scheduling solution would not be optimized for the construction industry, meaning you may find that it ends up being a “band-aid” solution.
Your construction business needs modern scheduling software designed to simplify the multifaceted nature of a construction project. It will help you drive operational efficiencies and streamline resource allocations through the entire lifecycle of the project.
Aristotle is credited with saying these famous words: “We are what we repeatedly do. Excellence, then, is not an act, but a habit.” Make it a habit to run successful projects with top-notch construction scheduling software.